Пайка магнію і магнієвих сплавів
На поверхні магнію так само, як і алюмінію і деяких інших металів, утворюється дуже тугоплавка окісна плівка. Щоб припій міг взаємодіяти з магнієм, цю окисну плівку необхідно або видалити...Бази для просторової розмітки
Поверхні заготовки готують до розмітки так само, як і при площинний розмітки. Заготівлю очищають від бруду, окалини, задирок, масла і перевіряють її розміри, порівнюючи з кресленням або зразком...Різка металу ручними ножицями
Ручні нотніци застосовують для розрізання сталевих листів товщиною 05 - 10 мм і з кольорових металів до 15 мм. Ручні ножиці виготовляють з прямими...Шабрування прямолінійних і криволінійних поверхонь
Шабрування прямолінійних (плоских) поверхоньДля отримання поверхні високої якості послідовно виконують чорнове, напівчистове і чистове шабрування.
Чорнове шабреніе (попереднє) полягає в грубій обробці поверхні: широкими шаберами видаляють сліди і ризики попередньої обробки. Спочатку з-за недостатньо ретельної підготовки поверхні окремі, найбільш виступаючі місця забарвлюватимуться густо і на...
Ручки напилків
Для тримання напилків вживають дерев'яні ручки. Обрана за розміром напилка ручка приганяють по його хвостовику, який повинен входити в неї на глибину від 2 /з до 3 /«довжини...Прийоми різання листового металу
Розрізати тонкий листовий метал можна двома способами. У першому випадку ножиці тримають в правій руці, вказівний палець поміщають між ручками (рис. 1). Розтискають (розкривають) ножиці мізинцем, безіменним і середнім пальцями. Лівою рукою утримують лист металу і подають його між лезами ножиць, направляючи лезо точно по ризику. Стискають ручки пальцями правої руки і розрізають заготовку. Потім повторюють операцію.При роботі ножиці слід розкривати не повністю, а лише настільки, щоб вони захоплювали листовий метал. Якщо розкрити ножиці занадто широко, то вони будуть не різати, а виштовхувати лист.
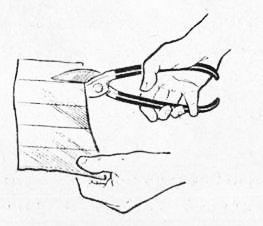
Мал. 1. Розрізання металу ножицями
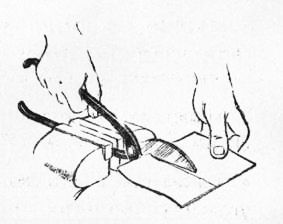
Мал. 2. Робота ножицями, затиснутими в лещатах
Другий спосіб полягає в тому, що одну ручку ножиць затискають в лещатах, а інша ручка залишається вільною. Послідовність роботи та ж, що і при першому способі, але рукою охоплюють лише одну ручку інструменту (рис. 92). Така установка ножиць дозволяє розрізати товщий метал і шматки більшого розміру з невеликими витратами зусиль.
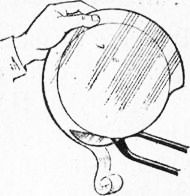
Мал. 3. Вирізання кола
...
Призначення просторової розмітки
Ви вже навчилися робити розмітку деталей за шаблонами, зразками, кресленнями в одній площині, тобто виконувати площинну розмітку. Але якщо у заготовок розмічаються кілька сторін, то розмітка називається...Зубчасті передачі
Зубчасті передачі є майже у всіх складальних одиницях промислового обладнання. З їх допомогою змінюють за величиною і напрямком швидкості рухомих частин верстатів, передають від одного вала до іншого зусилля і крутний момент.У зубчастої передачі рух передається за допомогою пари зубчастих коліс. У практиці менше зубчасте колесо прийнято називати шестернею, а більше - колесом. Термін «зубчасте колесо» відноситься як до шестерні, так і до колеса.
Зубчасте колесо, що сидить на ведучому валу, називають провідним, а сидить на відомому валу - веденим. Число зубів зубчастого колеса позначається буквою z.
Залежно від взаємного розташування геометричних осей валів зубчасті передачі бувають: циліндричні, конічні і гвинтові. Зубчасті колеса для промислового обладнання виготовляють з прямими, косими і кутовими (шевронними) зубами.
За профілем зубів зубчасті передачі розрізняють: Евола вентние і циклоїдальні. Крім зубчастих передач з Евола вентним зачепленням в редукторах застосовують передачу Новікова з круговим профілем зубів. Передача Новікова дозволяє застосовувати колеса з малим числом зубів, а значить, має велике передавальне число і може передавати значні потужності. циклоїдальний зачеплення використовується в приладах і годиннику.
Циліндричні зубчасті колеса з прямим зубом служать в передачах з паралельно розташованими осями валів і монтуються на останніх нерухомо або рухомо.
Зубчасті колеса з косим зубом застосовують для передачі руху між валами, осі яких перетинаються в просторі, а в ряді випадків і між паралельними валами, наприклад, коли в передачі повинні поєднуватися підвищена окружна швидкість коліс і безшумність їх роботи при великих передавальних відносинах до 15: 1.
Косозубі колеса монтують на валах тільки нерухомо.
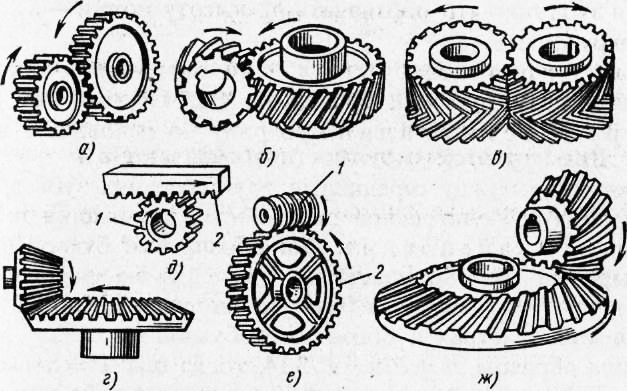
Мал. 1. Зубчасті зачеплення:
а - циліндричний з прямим зубом, б - те ж, з косим зубом, в - з шевронним зубом, г - конічний, д - колесо - рейка, е - черв'ячне, ж - з круговим зубом
Робота косозубих коліс супроводжується осьовим тиском. Осьовий тиск можна усунути, з'єднавши два косозубих колеса з однаковими, але спрямованими в різні боки зубами. Так отримують шевронне колесо (рис. 1 в), яке монтують, звертаючи вершину кута зубів в сторону обертання колеса. На спеціальних верстатах шевронні колеса виготовляють цілими з однієї заготовки.
конічні зубчасті передачі розрізняють за формою зубів: прямозубі, косозубиє і кругові.
На рис. 1 г показані конічні прямозубі, а на рис. 1 ж - кругові зубчасті колеса. Їх призначення - передача обертання між валами, осі яких перетинаються. Для пересічних осей застосовують також черв'ячні передачі (рис. 1 е). Конічні зубчасті колеса з круговим зубом застосовуються в передачах, де потрібна особлива плавність і безшумність руху.
На рис. 1 д зображені зубчасте колесо і рейка. У цій передачі обертальний рух колеса перетворюється в прямолінійний рух рейки.
Елементи зубчастого колеса. У кожному зубчастому колесі (рис. 2) розрізняють три кола (делительную, окружність виступів, окружність западин) і, отже, три відповідних їм діаметра.
Ділильна, або початкова, окружність ділить 3Уб по висоті на дві нерівні частини: верхню, звану головкою зуба, і нижню, звану ніжкою зуба. Висоту головки зуба прийнято позначати ha, висоту ніжки - hf, а діаметр кола - d.
Окружність виступів - це коло, що обмежує зверху профілі зубів колеса. Позначають її da.
Окружність западин проходить по підставі западин зубів. Діаметр цього кола позначають df.
Відстань між центрами двох сусідніх зубів, виміряний по дузі ділильного кола, називається кроком зубчатогозацепленія. Крок позначають буквою Р. Якщо крок, виражений в міліметрах, розділити на число л = 314 то отримаємо величину, звану модулем. Модуль висловлюють в міліметрах і позначають буквою т..
Дуга ділильної окружності в межах зуба називається товщиною зуба, дуга S1 - шириною западини. Як правило, S = = Sx. Розмір b зуба по лінії, паралельній осі коліс, називається довжиною зуба.
Радіальний зазор - найкоротша відстань між вершиною зуба і підставою западини сполученого колеса.
Бічний зазор - найкоротша відстань між неробочими профільними поверхнями суміжних зубів, коли їх робочі поверхні знаходяться в контакті.
З модулем пов'язані всі елементи зубчастого колеса: висота головки зуба ha = т, висота ніжки зуба hf = 12 т, висота всього зуба h = 22 т..
Знаючи число зубів z, за допомогою модуля можна визначити діаметр ділильної окружності зубчастого колеса d = zm.
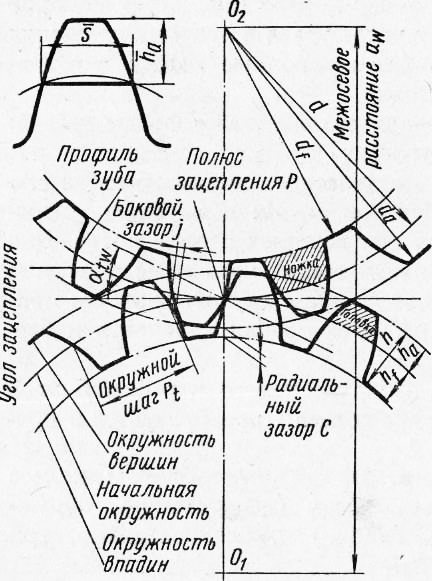
Мал. 2. Схема зачеплення в передачах циліндричними зубчастими колесами
Формули, за допомогою яких можна визначити параметри циліндричних зубчастих коліс в залежності від модуля і числа зубів, наведені в табл. 5.
Тихохідні зубчасті колеса виготовляють з чавуну або вуглецевої сталі, швидкохідні - з легованої сталі. Після нарізування зубів на зуборізних верстатах зубчасті колеса піддають термічній обробці, щоб збільшити їх міцність і підвищити стійкість проти зносу. У коліс з углеро-
дієтою CTa.'irf поверхню зубів покращують хіміко-термічним способом - цементацією і потім загартуванням. Зуби швидкохідних коліс після термічної обробки шліфують або притирають, Застосовується також поверхневе загартування струмами високої частоти.
Щоб зачеплення було плавним і безшумним, одне з двох коліс в зубчастих парах в окремих випадках, коли це дозволяє навантаження, виконують з текстоліту, древеснослоі-стого пластика ДСП -Г Або капрону. Для полегшення зачеплення зубчастих коліс при включенні за допомогою переміщення по валу торці зубів з боку включення заокруглені.
Зубчасті передачі бувають відкриті і закриті. Відкриті передачі, як правило, тихохідні. Вони не мають корпусу для масляної ванни і періодично змащуються густим мастилом. Закриті передачі укладені в корпуси. зубчасті колеса закритих передач змащуються або в масляній ванні, або струменевого мастилом під тиском.
За швидкохідності зубчасті передачі поділяються на такі види (м /с): дуже тихохідні - v < 0,5, тихоходные — 0,5 < v < 3, среднескоростные — 3 < v < 15, скоростные — 15 < v 40.
Точність виготовлення коліс і збірка передач повинні відповідати державному стандарту. Для циліндричних, конічних і черв'ячних зубчастих передач встановлено 12 ступенів точності, позначаються в порядку убування точності ступенями 1 -12.
Найбільш точні 1-я і 2-я ступеня є резервними, так як сучасні можливості виробництва і контролю не можуть забезпечити виготовлення точних коліс. 12-я ступінь також резервна, так як згідно з чинним ГОСТ ам зубчасті колеса поки не виконуються грубіше 12-го ступеня точності.
Велике застосування мають зубчасті передачі 678 і 9-го ступенів точності. Короткі характеристики найбільш поширених зубчастих і черв'ячних передач (6-й - 9-го ступенів точності) наведені в табл. 6. Кожна ступінь точності зубчастої передачі відповідає нормалі кінематичної точності, встановленої ГОСТ ом, а також плавності роботи колеса і контакту зубів.
Посадка зубчастих коліс на вали нічим не відрізняється від посадки шківів, тому нижче описана тільки перевірка, регулювання зубчастих і черв'ячних передач.
Основними технічними вимогами до зубчастих складальних одиниць є такі:
1. Зуби коліс при перевірці на фарбу повинні мати зону торкання не менше 03 довжини зуба, а за профілем - від 06 до 07 висоти зуба.
2. Радіальне торцеве биття коліс не повинно виходити за межі, встановлені технічними вимогами.
3. Осі валів зчіпних коліс і осі гнізд корпусів повинні лежати в одній площині і бути між собою паралельними. Допустимі відхилення вказані в технічних умовах.
4. Між зубами зчіпних коліс необхідний зазор, величина якого залежить від ступеня точності передачі і визначається за таблицею.
5. Зібрана складальна одиниця випробовується на холостому ходу або під навантаженням. Вона повинна забезпечувати відповідну міцність для передачі потужності, плавність ходу і помірний нагрів підшипникових опор (не більше 323 К, або 50 ° С).
6. Передача повинна працювати плавно і майже безшумно.
Нижче описаний порядок складання деяких складальних одиниць складових зубчастих коліс.
Зубчастий вінець встановлюють на центрирующий бурт А маточини і попередньо закріплюють трьома-чотирма тимчасовими болтами, що мають менший діаметр. Складальну одиницю перевіряють на оправці на радіальне биття і вінець закріплюють тимчасовими болтами. Решта отвори під болти в ступиці і вінці за допомогою кондуктора спільно розгортають і баньки, а потім в ці отвори вставляють нормальні болти, а тимчасові болти знімають і звільнилися отвори обробляють так само, як і перші. Після установки нормальних болтів в усі отвори зубчасте колесо остаточно перевіряють на биття. У важко навантажених передачах затягувати болти доцільно динамометричним ключем, щоб на площинах фланців створити силу тертя, момент якої перевищував би крутний момент, що передається зубчатим колесом.
Зубчастий вінець напресовують на диск маточини з натя-те. Щоб полегшити операцію і уникнути можливих перекосів, вінець попередньо нагрівають в масляній ванні або спеціальному індукторі т. В. ч. до 393-423 К (120-150 ° С). Потім свердлять отвори під стопори. замість стопорів нерідко кріплення здійснюють заклепками. У цьому випадку отвори свердлять наскрізь, встановлюють в них заклепки і розклепують на пресах.
При установці зубчастих складальних одиниць на валах найбільш часто зустрічаються такі похибки: хитання зубчастого колеса на шийці вала, радіальне биття по окружності виступів, торцеве биття і нещільне прилягання до наполегливої буртику вала.
на хитання складальну одиницю перевіряють обстукуванням напресованими зубчастого колеса молотком з м'якого металу.
Перевірку на радіальне і торцеве биття складальної одиниці - зубчасте колесо з валом виробляють на призмах або в центрах.
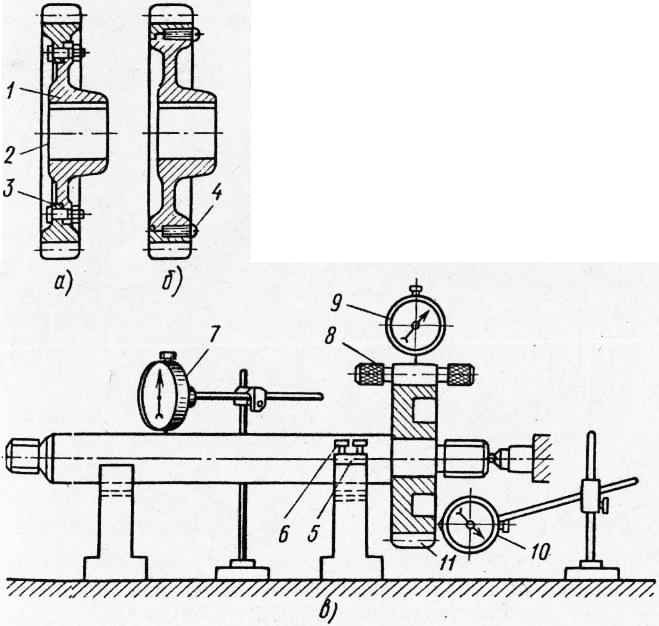
Мал. 3. Монтаж складових зубчастих коліс і перевірка на биття:
а - складене зубчасте колесо, закріплене болтами, б - закріплене стопорами, в - схема перевірка складальної одиниці вал - зубчасте колесо на радіальне і торцеве биття
Для цього вал укладають на призми, регулюють положення сідла призми гвинтами і встановлюють вал паралельно повірочної плиті по індикатору. У западину колеса укладають циліндричний калібр, діаметр якого повинен становити 168 модуля зачеплення колеса. Стійку з індикатором встановлюють так, щоб ніжка його увійшла в зіткнення з калібром і з натягом на один-два оберти стрілки. При цьому зауважують показання індикатора, потім, перекладаючи калібр через 2-3 зуба і повертаючи колесо, підводять калібр до ніжки індикатора. Відзначають показання стрілки і визначають величину діаметрального биття. Допустиме биття торця і діаметра вінця зубчастого колеса залежить від ступеня точності колеса по ГОСТ у. Торцеве биття перевіряють індикатором.
Правильне зачеплення зубів відбувається при паралельності осей коліс, відсутності їх схрещування і збереженні відстані між осями валів, рівного розрахункової величини. Паралельність розташування осей підшипників корпусу зубчастої передачі (рис. 4) перевіряють штіхмассом, штангенциркулем і індикатором. Відстань між осями підшипників перевіряють контрольними оправками, що встановлюються в корпус. Відстань вимірює або між оправками, або по їх зовнішньої поверхні.
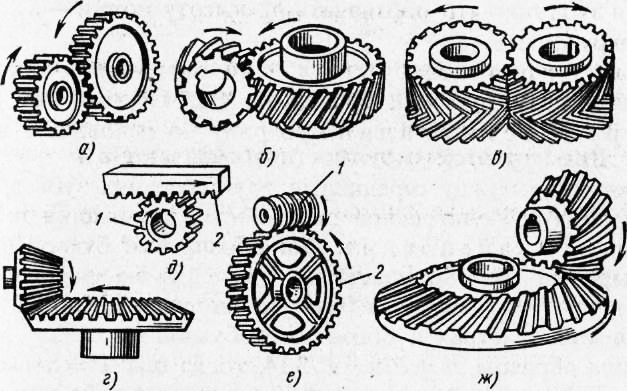
Мал. 4. Схема перевірки паралельності і перпендикулярності осей отворів і валів контрольним валом і універсальним вимірювальним інструментом
Визначивши розміри або на обох сторонах, встановлюють непаралельність осей отворів підшипників. Щоб добитися необхідного міжосьової відстані та паралельності, зміщують корпуси підшипників. Непараллельность у вертикальній площині може бути визначена при накладенні рівня на кожен з валів. Величина непараллельности в цьому випадку буде дорівнює різниці показань рівня в кутових розподілах. Зазвичай ціна ділення рівнів дається в частках міліметра на 1 мм і для перекладу показань рівня в кутові секунди ціну поділки потрібно помножити на число 200.
Наприклад, ціна ділення рівня 01 мм на 1 м відповідає 20 кутовим секундам (01-200 /1 = 20 ").
Від ступеня точності коліс і передач встановлюють норми бічного зазору. Основними є норми нормального гарантованого зазору (позначається буквою X), компенсуючого зменшення бічного зазору від нагрівання передачі.
На рис. 5 а показана перевірка бічного зазору, яку в циліндричних зубчастих колесах виконують щупом або індикатором. На валу одного з зубчастих коліс кріплять поводок, кінець якого наголошують в ніжку індикатора, встановленого на корпусі складальної одиниці. Інша зубчасте колесо утримують від провертання фіксатором. Потім поводок разом з валом і колесом злегка повертають то в одну, то в іншу сторону, а це можна зробити тільки на величину зазору в зубах. За свідченням індикатора визначають бічний зазор. Найменший бічний зазор С "вказують в технічних умовах на збірку складальної одиниці. При міжосьовій відстані 320 - 500 мм для передач середньої точності зазор цей повинен бути не менше 026 мм. Найбільш точно бічні зазори вимірюють за допомогою індикаторних пристроїв так званим виносним методом. Пристосування дозволяють проводити виміри зазору в глухих передачах.
На рис. 5 б показано одне з таких пристосувань. Воно складається з хрестовини, закріпленої на валу редуктора рукоятками, і стійки з індикатором. Стійку з індикатором ввертають в хомут, закріплюють гвинтом до кришки редуктора. При погойдуванні вала рукою до зіткнення площині хрестовини з ніжкою індикатора, закріпленого на нерухомій кришці редуктора, визначають бічний зазор між зубами. Мале колесо передачі повинно бути нерухомим.
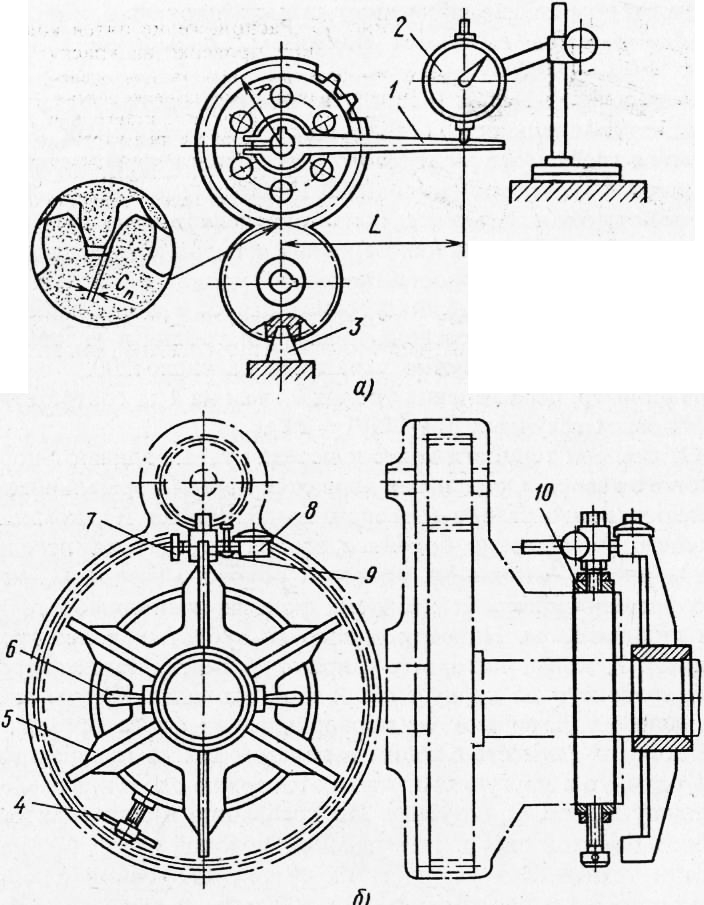
Мал. 5. Схема перевірки бокового зазору індикатором: а - відкритим способом, б - виносним
Заміряний зазор слід віднести до діаметру початковій окружності зубчастого колеса, на валу якого закріплена хрестовина.
Таким же чином перевіряють бічний зазор і для інших п'яти положень хрестовини, при повороті її разом з валом на кут 60 °. За результатами вимірів визначають коливання величини бічних зазорів і судять про якість зібраної передачі. Залежно від модуля і точності зубчастої передачі допустима різниця бічних зазорів становить 008-015 мм.
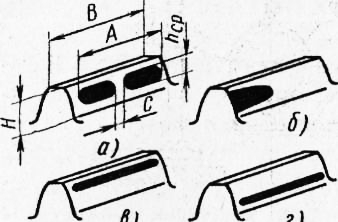
Мал. 6. Розташування плям контакту при перевірці на фарбу:
а - розміри контакту для оцінки, б - одностороннє розташування плями (перекіс колеса на зуборізна верстаті або перекіс отворів в корпусі редуктора, в - великий зазор по всьому вінця (мало або велике міжосьова відстань), г - недостатній зазор по всьому вінця (зайва або недостатня товщина зуба одного або обох коліс)
неправильне пляма торкання і неправильне місце розташування на зубах є наслідком похибок, що виникли при опрацюванні та складанні коліс, валів, корпусів редукторів, підшипників. на рис. 6 б відбиток фарби розташований односторонньо. Причиною неправильного плями контакту може бути перекіс колеса на зуборізна верстаті або перекіс отворів в корпусі редуктора.
Якщо зуб колеса втоплений з боку торця і при поверненні на 180 ° становище не змінюється, то, отже , перекошена вісь отвору в корпусі. Цю похибка усувають запрессовкой нової втулки і розточування її або Перепресовка пальця зубчастого колеса, якщо воно посаджено на палець.
На рис. 6 в показаний занадто великий зазор по всьому вінця. Можливі причини: міжосьова відстань в корпусі недостатнє або занадто велике. Усувають похибка
Перепресовка втулок в корпусі і їх повторним розточуванням.
Недостатній зазор по всьому вінця показаний на рис. 6 м Можливі причини малої величини зазору: зайва або недостатня товщина зуба у одного або у обох коліс. У цьому випадку заміняють колеса або використовують корпус з іншим міжосьовим відстанню.
...
Гази, обладнання та апаратура
Правила застосування та поводження з газами і газовою апаратурою детально розглянуті в Американському Стандарті Z 49. 1.Устаткування, інструменти і шланги необхідно...
Робота зі сталями
Сталями називаються сплави заліза з вуглецем, що містять до 17% вуглецю.Залежно від хімічного складу стали бувають вуглецеві і леговані.
У вуглецевих сталях основним легуючим елементом є вуглець. Леговані стали, крім того, містять спеціально введені легуючі елементи (хром, нікель, молібден, вольфрам), що поліпшують їх властивості.
Вуглецеві сталі
За способом виробництва сталі бувають мартенівські, бесемерівську (конверторні), електросталі і ін. При маркуванні стали спосіб виробництва вказують буквами: М-мартенівська, Б - бесемерівську. Наприклад, Мст.З - сталь мартенівського виробництва.
За ступенем розкисленням стали діляться на киплячу, спокійну і полуспокойную.
Кипляча сталь (КП) в повному обсязі розкислення в печі і при розливанні продовжує кипіти.
Спокійна сталь (СП) повністю розкислення. Вона відрізняється кращою якістю, ніж кипляча. Має більш однорідну будову, менше схильна до старіння і переходу в крихке стан при роботі на морозі.
Пол # спокійна сталь займає проміжне положення.
За якістю сталь буває звичайна і якісна.
Сталь звичайної якості поставляється по ГОСТ у 380-60. Залежно від призначення і гаранта-ються характеристик сталь підрозділяється на три групи.
Група А поставляється за механічними властивостями.
Група Б поставляється за хімічним складом.
Група В поставляється за механічними властивостями і хімічним складом.
Якісна сталь ( ГОСТ 1050-60) в порівнянні зі сталлю звичайної якості містить знижена кількість шкідливих домішок сірки і фосфору.
Якісні вуглецеві сталі маркуються цифрами, що позначають середній вміст вуглецю в сотих частках відсотка. Наприклад, ст. 10 ст. 15 і ст. 25 містять відповідно десять, п'ятнадцять і двадцять п'ять сотих відсотка вуглецю. Крім стали з нормальним вмістом марганцю (025-080%) до якісних вуглецевої сталі відносяться сталі з підвищеним вмістом марганцю (070-120%) марок 15Г, Зог , 60Г, а також стали, леговані сотими частками Відсотка бору, титану і цирконію (08Т, ЗОТ, 40Р).
За змістом вуглецю розрізняють наступні види стали:
низьковуглецевих сталі (до 025% вуглецю) термообробкою незміцнюється. Температури відпалу і нормалізації їх - 880-890 °.
Середньовуглецеві стали (від 026 до 045% вуглецю) піддаються термічній обробці.
Високовуглецеві стали (від 046% вуглецю) при мідницьким-жестяницкие роботах не застосовують.
Леговані стали
За змістом легуючих елементів стали діляться на низьколеговані, середньолеговані і високолеговані. Низьколегованісталі ( ГОСТ 5058-57) містять до 2% кожного легуючого елемента при сумарному змісті легуючих не більш як 5%; середньолеговані Стали ( ГОСТ 4543-61) від 2 до 5% кожного легуючого елемента, при сумарному змісті від 5 до 10%; високолеговані сталі ( ГОСТ 5632-61) -Кожному легуючого елемента не менше 5% при сумарному змісті понад 10%. За призначенням сталі бувають конструкційні, інструментальні, шарікоподшипниковиє, корозійностійкі (нержавіючі), жаростійкі.
Маркуються стали буквами і цифрами: перша цифра, що стоїть перед буквами, позначає вміст вуглецю в сотих частках відсотка, букви - легуючі елементи, а числа після букв - приблизний зміст елемента, якщо воно перевищує 1%.
Для легуючих елементів прийняті наступні позначення: Б -ніобій, В -вольфрам, Г - марганець, Д - мідь, К - кобальт, М - молібден, Н - нікель, Р - бор, С - кремній, Т - титан, Ф - ванадій , X - хром, Ю - алюміній.
Буква А в кінці маркування означає, що сталь містить знижена кількість сірки і фосфору і є високоякісною. Наприклад, сталь 18Х2Н4ВА містить 018% вуглецю, 2% хрому, 4 ° /о нікелю і менше 1% вольфраму. Сталь високоякісна.
В інструментальних сталях перша цифра показує вміст вуглецю в десятих частках відсотка. Швидкорізальної сталі позначають буквою Р і цифрою, що показує вміст в них вольфраму. Леговані стали при мідницьким-жестяницкие роботах застосовують рідко, за винятком нержавіючої сталі типу 1Х18Н9Т, термообробка якої полягає в загартуванні при температурі 1050-1100 ° в воді або на повітрі.
...
Способи просторової розмітки
Установка заготовок на розмічальній плиті. Перед установленням заготовки на розмічальній плиті ті місця заготівлі, де будуть наноситися розмічальні ризики забарвлюють крейдою, фарбою, лаком або мідним купоросом. При установці тільки перше положення заготовки на плиті є незалежним; всі інші положення залежать від першого. Перше положення деталі потрібно вибрати так, щоб було зручно почати розмітку від поверхонь або центрових ліній, прийнятих за базу. Наприклад, для розмітки нижній частині підшипника, зображеного на рис. 2 а, за базу необхідно прийняти нижню поверхню його заснування. Отже, підшипник треба встановити на плиті так щоб ця площину була паралельна площині плити.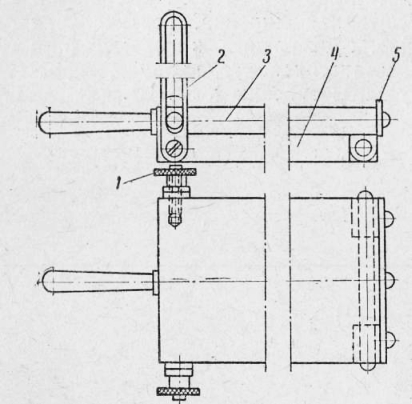
Мал. 1. Шарнирная плита для розмітки
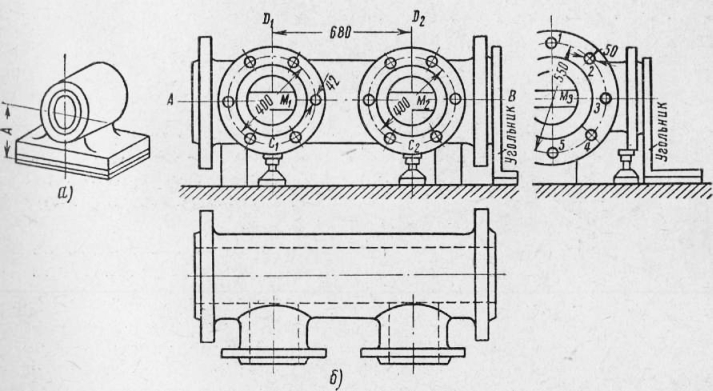
Мал. 2. Вибір бази при просторової розмітки
При розмітці патрубка доцільно прийняти за основу центри його фланців. Тому патрубок потрібно встановити так, щоб першу ризику можна було провести за центрами фланців. Одночасно при установці патрубка потрібно перевірити косинцем перпендикулярність поверхні...
Центрування заготовок при свердлінні
Центрові отвори в торці заготовки спочатку свердлять коротким свердлом діаметром 2-3 мм на глибину приблизно 6 мм, а потім раззенковивают їх зенковкой з кутом 60 ° по діаметру 5 мм.Але є й інший спосіб: за допомогою комбінованих центровочних свердел. Цей інструмент як би поєднує спіральне свердло і конічну зенковку. Центрування таким інструментом набагато продуктивніше і легше, ніж спіральним свердлом і зенковкой.
Центрові отвори свердлять на токарному верстаті в такий спосіб. Деталь кріплять в трикулачні патроні, а в піноль задньої бабки встановлюють патрон з комбінованим свердлом. Подаючи свердло вручну (обертанням маховичка), виконують центрове отвір.
...
Свердла, що не мають визначеності базування
Розглянемо свердла, що працюють методом поділу подачі і призначені для швидкісного свердління. Свердла інших конструкцій для нешвидкісного свердління докладно описані в роботах.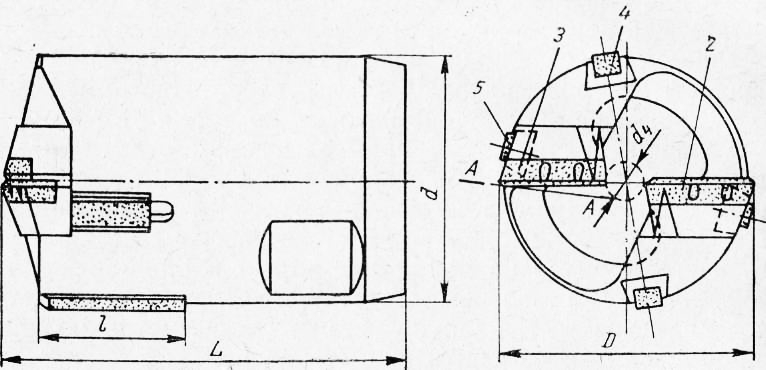
Мал. 1. Свердел для швидкісного свердління, що працює методом поділу подачі:
1 - корпус; 2 3 - різці; 4 5 - напрямні; 6 - гвинт
Створенню конструкції описуваного свердла передувало проведення значного обсягу експериментальних робіт і випробування численних варіантів конструкцій свердел.
При розробці свердла даної конструкції були поставлені такі основні завдання:
1) підвищити продуктивність свердління в порівнянні зі свердлами існуючих конструкцій;
2) збільшити надійність роботи свердел на швидкісному режимі свердління;
3) знизити вартість інструменту;
4) полегшити умови експлуатації свердел.
На перший погляд завдання здавалися досить простими, так як наявні одно-, дво- і трехрезцовие свердла забезпечували продуктивність свердління при налагодженому процесі близько 5-6 м /ч. Для подальшого збільшення продуктивності свердління (в два-три рази).
Виготовити таке свердло найпростіше було припаюванням різців до їх корпусу, а так як три або дві ріжучі кромки важко розташувати у центру різця, то свердло слід робити кільцевим.
Такі свердла були виготовлені і випробувані. Вони показали рекордну продуктивність, але низьку надійність в роботі. Крім частих Викришування різальних крайок, у них під час свердління з'явився новий дефект - огранювання. Свердління вимагало ретельного відпрацювання процесу. Особливо важко проходило врізання і вихід інструмента із заготовки. Складність ремонту пошкоджених свердел змусила повністю відмовитися від безпосереднього при-паіванія твердого сплаву різців і напрямних до корпусу свердла.
Трехрезцовие свердла виявилися занадто ажурними, так як в передньому торці корпусу потрібні були три вхідних отвори під стружку. Тому нове свердло вирішено було зробити дворізцевій, зі змінними різцями і направляючими, а ріжучі кромки розташувати по одному діаметру.
Спочатку не зовсім ясно було з висвердлюють стрижнем.
Досвід кільцевого свердління показував, що висвердлюють стрижень ускладнює нормальний перебіг процесу свердління, так як займає в стеблі центральну частину. Якби свердління проводилося свердлом для суцільного свердління, то відходить стружка мала б можливість перерозподілятися по перетину стружкоотвода за рахунок центральної порожнини стебла, так як з цієї частини видаляється матеріалу утворюється найменшу кількість стружки. При кільцевому же час свердління в зазор між висвердлюють стрижнем і внутрішньою поверхнею стебла надходить велика кількість стружки.
При збільшенні діаметра висвердлюється стрижня зазор з для підведення охолодження, як правило, не змінюється, а товщина стінки стебла може змінюватися тільки незначно, так як при великій глибині кільцевого свердління стебло повинен бути жорстким. Тому збільшення діаметра висвердлюється стрижня призведе до різкого скорочення перетину кільцевої порожнини всередині стебла, по якій повинна вимиватися стружка. З цього випливає, що збільшення діаметра стержня викликає необхідність ретельного подрібнення стружки (і по довжині і по ширині), а також неминуче призводить до підвищення робочого тиску рідини, транспортує стружку.
Ще більшу незручність при кільцевому свердлінні виникає при великих діаметрах висвердлюють стрижнів. Дуже часто
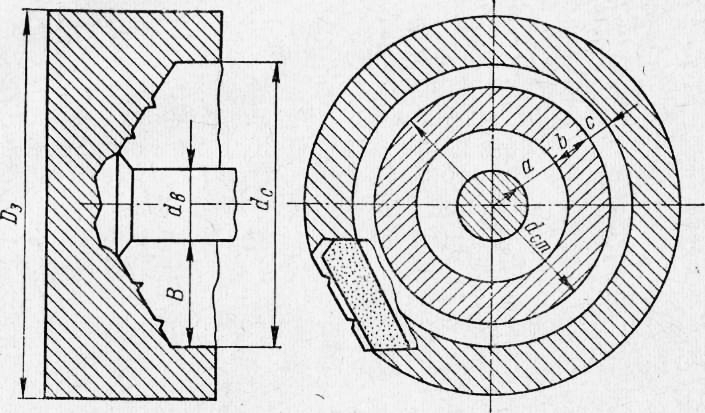
Мал. 2. Перетин заготовки під час свердління свердлами, показаними на рис. 1
стрижень внаслідок перерозподілу внутрішніх напрузі в матеріалі заготовки піддається значному викривлення. У цьому випадку він чинить тиск на внутрішню поверхню стебла, зношуючи її. Іноді подібне явище може виявитися причиною порушення стружкоотвода, так як відходить стружка може заклініваться між стеблом і пошкодженим стрижнем. Особливо неприємно виводити і вводити свердло, коли покороблена стрижень. Введення свердла, як правило, в таких випадках проводиться не одним, а двома операторами.
Для боротьби з викривленням стрижня великого діаметра застосовують іноді спеціальні підтримки. Підтримка повинна вставлятися в розточене отвір передбачуваного стрижня до початку кільцевого свердління. Розточування отвору, закріплення підтримки і маніпулювання з нею після завершення проходу викликають додаткові витрати часу і тому її намагаються по можливості не застосовувати.
Такі розміри стержня при роботі свердел дали наступні переваги:
1) забезпечили відхід від «нульової» швидкості і зони великих пластичних деформацій, які викликали б відколи твердосплавних різців в центральній зоні свердла;
2) не жорсткий стрижень не зношується стебло свердла і не ускладнює в разі необхідності проходу новим свердлом вхід інструменту в отвір;
3) полегшується стружкоотвода, а отже, не підвищується тиск робочої рідини;
4) при свердлінні глухих отворів витяг стержня не представляє особливих труднощів, так як його можна легко відокремити від заготовки.
Таким чином, прийняті розміри висвердлюють стрижнів підвищують надійність роботи нових свердел (рис. 1) і покращують їх експлуатаційні властивості.
Вузлом свердла, в якому вимагали численних доробок, є також різці та їх сполучення з корпусом свердла. Для створення жорсткого з'єднання різців з корпусом свердла і забезпечення точності установки без додаткових прігонок і регулювань довелося відмовитися від компенсаторних прокладок і розташування осей хвостовиків різців під кутом до осі свердла. Було вирішено виготовляти різці з круглими хвостовиками, як у дво- і трехрезцових свердел. Однак звичайні хвостовики, маючи пару з корпусом свердла по посадці недостатньо зручні в експлуатаційному відношенні (то хвостовики різців «провалюються» в корпусі свердла, то доводиться їх забивати в корпус свинцевими, латунними, а іноді і звичайними сталевими молотками). При вивченні заводських свердел у багатьох різців на передньому торці державки була із слідами ударів і деформації матеріалу. Сполучення ж хвостовиків різців з зазорами також передчасно виводило різці з ладу. Було відмічено, що корпуса свердел виходили з ладу через розробку посадочних гнізд під різці.
Все це призвело до конструкції різців з цанговим розтуляючи хвостовиків і асиметричним розташуванням головки різців щодо хвостовиків.
Цанговий разжим хвостовиків вставних різців значно підвищує культуру експлуатації свердел. Різці вільно встановлюються в корпусі свердла до упору в базову стінку, а потім викруткою розтискується хвостовик з боку задньої частини свердла. Корпус при постановці різців не зношується, так як «пелюстки» хвостовика при введенні в корпус свердла знаходяться в неразжатом положенні.
При заміні різців необхідно тільки вивернути трохи разжимной гвинт, і різець вільно виходить з корпусу свердла.
Істотне значення при базуванні різця в корпусі свердла має асиметричне розташування головки різця щодо хвостовика. В результаті цього головка різця завжди щільно притиснута силами різання до опорної майданчику корпусу свердла, особливо в зоні периферійної ріжучої кромки. У центральній частині свердла різці підтримуються хвостовиками.
Прийнята конструкція вузла різців дозволила проводити загострювання різців окремо від корпусу свердла за допомогою спеціальної оправлення, на якій група різців (10-20 шт. І більше) шліфується по всьому ріжучого контуру з однієї установки. Шліфувальний верстат налаштовується послідовно для шліфування всіх елементів ріжучого контуру різців. Після шліфування різці проходять заточку кутів різання окремо від оправлення. При цьому у ріжучого контуру необхідно залишати контрольні стрічки шириною не більше 005 мм.
В результаті такої роздільної заточки для групи шліфованих одночасно різців забезпечується взаємозамінність їх. Слід мати на увазі, що половина з заточуваних різців на передньому торці повинна мати стружкоразделітельние канавки, розташовані зі зрушенням щодо переднього торцадругой половини різців. Тому правильніше говорити про взаємозамінність пар різців. Парні різці повинні мати відповідні клейма для забезпечення комплектації і збірки свердел.
Ідея створення групової оправлення для шліфування ріжучих контурів різців виникла при вирішенні питання про заточуванні центральних калібрують крайок різців, що оформляють висвердлюють стрижень. Було ясно, що заточувати центральні стандартизації цих величин кромки різців в зборі зі свердлом нераціонально, так як для цієї операції було б потрібно шліфувальний круг діаметром dm = (01бн-02) dc. Подібний коло не зміг би забезпечити нормальну продуктивність, вимагав високошвидкісний привід і в роботі швидко зношувався.
З огляду на ці обставини, була виготовлена оправлення для групового шліфування різців (рис. 3).
З малюнка видно, що різці, діаметрально розташовані на оправці, мають значно більші осьові відстані, ніж різці в корпусі свердла. Це стало можливим завдяки зміщенню головних різальних крайок різців уздовж утворюючих конічної поверхні, що є поверхнею різання під час свердління.
Оправлення для групового шліфування різців уможливила застосовувати практично будь-який діаметр кола для шліфування центральних крайок, калібрують стрижень. Це, в свою чергу, збільшило і продуктивність їх шліфування.
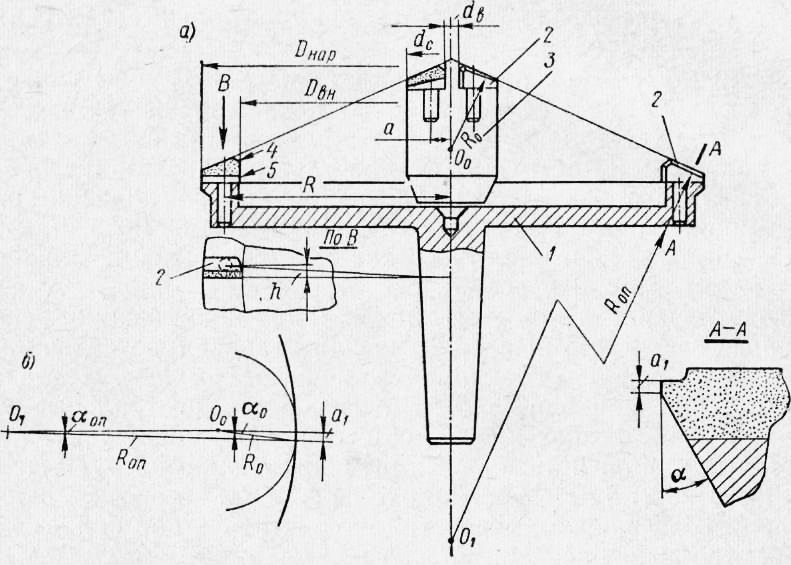
Мал. 3. Оправлення для групового шліфування контуру різців (а) і схема зміни заднього кута різців при заточуванні в оправці (б)
Цей захід допомагає скоротити як час на переточування (перешлифовки), так і витрата твердого сплаву.
Корпуси свердел виготовляються досить точно і їх форма технологічна. Опорні стінки для різців шліфуються «на прохід». Отвори під хвостовики різців розточуються з допуском, що не перевищує ± 5 мкм, і виготовляються, як зазначалося вище, з осями, паралельними осі свердла. Це дозволяє розточувати гнізда під різці з однієї установки корпусу при переміщенні заготовки тільки по одній координаті або при його повороті на кут 180 °. Все це полегшує обробку корпусу, проте не вирішує питання про компенсацію розміру отвору при переточуванні різців. В ряді випадків, коли до розмірів просвердлюють отвір не пред'являються жорсткі вимоги, це питання відпадає. Але іноді необхідно витримувати діаметр свердління в межах 5-го і навіть 4-го класів точності. Для цього випадку було запропоновано виготовляти корпуси декількох розмірів, що відрізняються один від іншого тільки відстанями між осями отворів під хвостовики різців (а).
У великосерійному або масовому виробництві виготовлення декількох корпусів свердел для глибокого свердління не становить труднощів і може бути виправдано так само, як ремонтні розміри поршнів, сорочок, циліндрів та інших швидкозношуваних деталей при експлуатації автомобілів і тракторів.
Для запобігання корпусу свердла від зносу і для сприйняття випадкових навантажень під час свердління корпус забезпечений чотирма твердосплавними напрямними: двома довгими і двома короткими. Ці напрямні, крім вищевказаного призначення, утворюють зазор між свердлом і отвором для підведення охолоджуючої рідини. Якби вони були відсутні, то на корпусі свердла довелося б фрезерувати спеціальні пази для підведення рідини. Наявність вставних напрямних значно полегшує зовнішню обробку корпусу свердла. Посадка напрямних в корпус виробляється, як і у свердел з певністю базування, на ластівчин хвіст.
Так як на практиці знос направляючих, як правило, відсутня, то виникає питання, чи варто взагалі застосовувати напрямні і які вони повинні бути - жорсткі або пружні. Якщо застосувати жорсткі направляючі, то чи не буде корпус свердла при зносі периферійних калібрують крайок заклініваться в просвердленому отворі. На ці питання відповісти ще важко, так як недостатньо накопичено фіктіческій матеріал. Кілька випадків випробування свердел різної конструкції представляють в цьому відношенні великий інтерес.
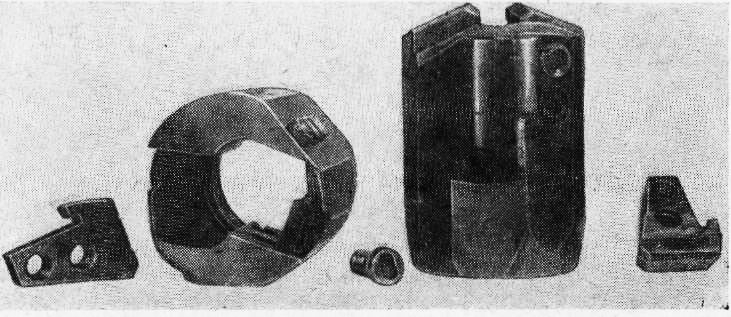
Мал. 4. Дослідне свердло з нежестким кріпленням ріжучих пластин
При вирішенні питання про форму різців для нових свердел один з варіантів свердел випробовувався з жорсткими пластинами, які передбачають можливість компенсації зносу периферійних різальних крайок свердла (рис. 4). Незважаючи на гадану надійність даної конструкції, виявилося, що пластини під час свердління «Здавали» - переміщалися під кутом відносно корпусу, а працювати замість калібрують периферійних кромок поступово починали жорсткі направляючі корпусу свердла. При цьому ватметр показував помітне зростання потужності, а заготівля сильно перегрівалася. Кожен досвід свердління закінчувався спрацьовуванням теплового реле і вимиканням двигуна приводу.
Досліди повторювалися кілька разів, так як робилися спроби усунути нежорстке кріплення змінних пластин. Крім того, було відмічено, що ріжучі кромки свердла після дослідів перебували в чудовому стані. Стружка мала блискучу поверхню і якби не зростання потужності і спрацьовування запобіжників, то перебіг процесу можна було б визнати вельми сприятливим, в той час як зростання потужності показувало надопустімое заклинювання напрямних свердла.
Цей досвід вказував на необхідність проектувати більш жорсткі з'єднання різців з корпусом свердла.
Ідея створення жорсткої посадки інструменту в обробленому отворі викликала поява кількох нових конструкцій інструментів і напрямних до них, які втілилися потім в «пружні» муфти. Цікаво відзначити, що описані досліди, проведені тими ж свердлами, але без напрямних, завжди закінчувалися Викришування різальних крайок. Випробування нових свердел з чотирма направляючими, заниженими щодо периферійних кромок різців на Ad = 01 ч-02 мм, показали задовільні результати. Незважаючи на тривале застосування свердел, не було жодного випадку їх заклинювання в отворі заготовок.
Шліфування напрямних 4 виробляється в зборі з корпусом свердла. Для якісного і продуктивного виконання цієї операції застосовується спеціальне облямовування 1 (рис. 35), на яку нагвинчується корпус свердла 3. Під час шліфування оправлення базується на центри круглошлифовального верстата і приводиться в обертання повідцем, закріпленим на лиски 2. При цьому центри верстата повинні бути нерухомими.
Раніше багато різновидів свердел заточувалися і шліфувалися при консольному закріпленні спеціальних оправок, зазвичай мають в якості елемента приєднання конус Морзе. Консольне кріплення інструменту на шпинделі в більшості випадків не забезпечує ні якісного, ні продуктивного проведення заточувальних операцій. Тому воно по можливості повинно бути замінено на беськонсольниє кріплення.
Контроль заточування свердел для глибокого свердління середніх діаметрів на багатьох заводах проводився до недавнього минулого за допомогою шпиндельних пристроїв, що дозволяють закріплювати свердло (свердлильну головку) і повертати його навколо осі. Як вимірювача застосовувався індикатор. При переході до свердла, що працюють методом поділу подачі, вимоги до більше, чим більше буде перевищення однієї ріжучої кромки над іншою.
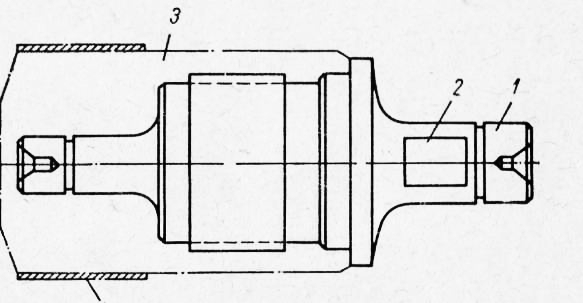
Мал. 5. Оправлення для шліфування напрямних свердла, наведеного на рис. 1
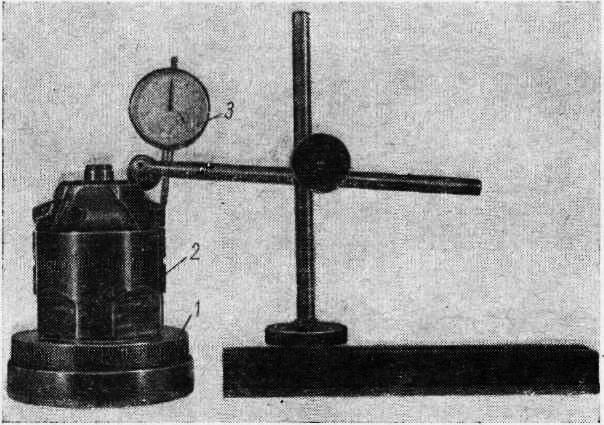
Мал. 6. Установка для контролю свердел і розточувальних головок:
1 - шайба контрольна; 2 - ріжучий інструмент (свердла, розточувальні головки); 3 - індикатор
Шпиндельний прилад в цьому випадку не годиться, гак як він допускає неточність близько 002 мм, а конусна оправлення і посадочне місце під свердло подвоюють цю похибку. Тому довелося змінити спосіб базування свердел при контролі.
В даний час для базування свердла при контролі застосовується досить простий спосіб. Свердло встановлюється у вертикальне положення на контрольну шайбу, що центрує поясок якої виготовлений по ковзної посадці 2-го класу точності. Робочий торець шайби обробляється за одну установку з пояском. При контролі свердло або розточна головка базуються на контрольній шайбі заднім торцем і заднім центрирующим пояском у різьблення (рис. 6). Різьба, центруючі пояски і задній торець свердла обробляються також за одну установку.
Великою перевагою цього способу контролю є висока точність базування, простота і дешевизна контрольних шайб.
Перші випробування нових свердел (рис. 1) підтвердили результати раніше проведених дослідів з трехрезцовимі свердлами. Позначалася відсутність визначеності базування. Після кожного свердління виявлялися сліди органкі. І тільки після того як була застосована пружна муфта (див. Гл. IV), процес свердління став стабільним як по продуктивності, так і за якістю. Стало ясно, що нові свердла можуть мати продуктивність, що перевищує значно середню швидкість проходу, зазначену вище. Однак випробування проводилися під час свердління порівняно коротких зразків (12-15) м, виготовлених з нормалізованої сталі 35. Тому виникали сумніви, що під час свердління довгих заготовок з легованих сталей нові свердла дадуть великі відведення.
Випробування нових свердел на довгих заготовках пройшло досить успішно. Нові свердла при цьому показали наступні переваги:
1) високу стійкість: свердло без переточування пройшло отвір 080 мм на довжину більше 18 м
2) високу продуктивність: швидкість годинного проходу становила s4> 15 м /ч;
3) малі відведення: 05 мм на 1 м довжини свердління;
4) відсутність огранки на поверхні просвердлених отворів;
5) чистота обрабатанной поверхні отворів була вище V5 і місцями перевищувала V7;
6) поперечні розміри просвердлених отворів перебували в межах допусків Л4-АЬ.
Як і до цього, знос направляючих майже відсутній. Свердління проводилося на сульфофрезол при одночасному обертанні заготовки і стебла зі свердлом. Заготовки при випробуванні не мали отворів під візит інструменту. Тиск охлаждающе-змащую-щей рідини не перевершувало 5-8 кг /см2.
Для випробування свердел був виготовлений новий стебло довжиною близько 14 м. Цей стебло був складений з окремих труб, довжиною по 2 м. З'єднання труб вироблялося зварюванням. Труби при цьому мали центруючі елементи і фаски під зварні шви. Після зварювання стебло проходив додаткову обробку швів (зачистку) і рихтування, яка, однак, була проведена недостатньо ретельно. Під час роботи стебло встановлювався в пружне ланка редуктора, в чавунні вкладиші проміжних підтримуючих стійок і через пружну муфту з'єднувався зі свердлом. Спочатку свердління стебло бив, але через кілька хвилин після початку свердління, перебуваючи в контакті з чавунними добре змащувати вкладишами проміжних стійок, повністю припинив биття. Таким чином, рихтування стебла відбувалася паралельно свердління.
Випробування свердел практично підтвердили придатність методу розподілу подачі при швидкісному глибокому свердлінні як по продуктивності і якості, так і по економічності процесу. Свердла легко збиралися, порівняно просто Переточувати і за вартістю були конкурентоспроможними з дво- і трехрезцовимі свердлами. Процес швидкісного свердління глибоких отворів новими свердлами вимагав тільки високої культури в підготовці і проведенні операції, так як швидкості обробки, які застосовувалися при цьому, вимагали відповідних навичок від операторів.
...
Інструменти для нарізування внутрішньої різьби в металі
Основними інструментами для нарізування різьблення є мітчики і плашки.Мітчиком називається ріжучий інструмент, призначений для нарізування різьблення...
Залишки масляних або жирових пастоподібних флюсів
Залишки масляних або жирових флюсів-паст зазвичай видаляють органічними розчинниками.Паяльні пасти є емульсії вазеліну і водних розчинів хлоридів цинку і амонію. Через корозійних...